In the manufacturing landscape, automated material handling systems ensure that products get moved from one place to another with extreme efficiency. It can happen within the same floor or another department of the manufacturing unit or even in a completely new building in which manufacturing production is taking place. By taking the help of process step information and routes, automated material handling systems move materials with the help of conveyors, autonomous vehicles or vertical elevators.
It is safe to mention that this kind of technology is extremely efficient when it comes to improving the flexibility of manufacturing work. Let us discuss all the advantages that could be obtained from using such innovation.
What are the main functions of automated material handling systems?
The automated material handling systems (AMHS) are fundamentally known to leverage carrier and material tracking systems to identify materials that have been placed at a pick-up point by their operator. It is also known to process the material identifier and also select the next destination to further transport the materials to the same. One of the main features of an automatic material handling system is that irrespective of the mode of transport; the systems are perceived to work best when a substantial amount of information is available and visible to the staff working within the manufacturing unit.
In addition to that, in a fully implemented automated material handling system, no interaction between humans and the carriers, materials or transport system would be prevalent. The reason is that the automated material handling system is capable of handling all the information alone by identifying the routing and material delivery to the most appropriate tools.
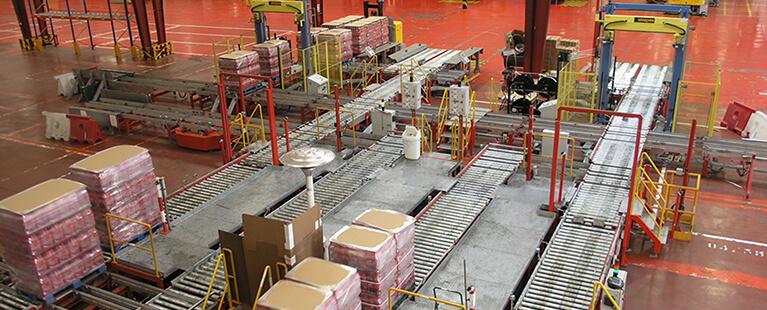
What are the main benefits of automated material handling systems?
A manufacturing unit is made up of several steps that are extremely important and represents the life cycle of materials that are required to be transported to each of the next steps. However, if all this work is done by humans, then it might become extremely costly, repetitive and inadequate utilisation of labour. In that context, automated material handling systems attempt to solve all these problems and offer the following benefits.
Efficiency in data access
To handle materials that function independently of one another, an industry has a variety of workplaces and tools. Automation of this isolation equipment would enable the creation of integration systems, logistics experts, facility management, and the instantaneous data delivery of all other industry employees. This technology makes it possible for employees to communicate with one another inside the company.
A networked conveyor system may easily change the product flow at a distribution centre. Based on the environment and the components that need maintenance, this is done. As a result, workers and machines would operate efficiently and in accordance with one another. Several areas of the institution can plan their next moves with this knowledge in order to prevent delays and even bring about change.
Improved quality control
Automated material handling systems can be used effectively to inspect an error. This automated error checking lowers the likelihood of waste output and rework. The most effective automated machines that expertly inspect faults are offered by material handling automation firms like Armstrong.
Because of their effectiveness, automated machines are becoming more and more well-known. Manufacturing processes are more effective and simple thanks to automated equipment, and all items are of higher quality now than they were in the past when mistakes were ignored.
Workplace safety
The use of automated material handling systems increases workplace safety and cuts down on the amount of time needed to execute challenging jobs. This has occurred as a result of the usage of automated trucks and robot arms in place of human ones. By properly separating a man from a machine at work, this technology assures the worker’s safety at their place of employment.
The use of more sophisticated sensors and laser-guided technology has contributed to the development of a quality-controlled workplace that boosts productivity without endangering anyone.
Flexible production
Production has improved in flexibility because of automated material handling technologies. Without wasting a second, they are equipped to produce a variety of goods. Giving supply chains and logistic managers the choice of how to process the data gives operations flexibility.
Adequate use of labour
There is a labour cost associated with transferring an item to its next location when that location is in a different building, department, or area of the same building. Based on the subsequent step in the process flow as specified in the manufacturing execution system (MES), transport systems can move material to its next location.
The carrier is simply placed on a transport system receiving port by the operator, who then exits the area. The operator doesn’t have to leave their designated station to complete their present activities because the AMHS will take care of the rest.
Less contamination
Some industrial settings are vulnerable to airborne contaminants that can be easily agitated by human movement and ultimately taint the product being produced. As a result, initiatives to minimise pointless movement can aid in particulate-sensitive workplaces like the semiconductor manufacturing process.
Adherence to regulations
Companies must abide by laws that set limits on how much weight an employee is allowed to lift on their own. AMHSs may be given “the heavy lifting.” Additionally, AMHSs are less likely to mishandle a heavy pod of pricey material because they don’t require breaks, request vacations, get sick, or need breaks at all.
Conclusion
Last but not least, you should think about how your staff feels about automated material handling systems. When the automated material handling systems offered by Godrej Koerber are first put into place, they can be perceived as invading the space and threatening the livelihood of your employees and floor operators because they will be tasked with performing the repetitious and unglamorous but essential jobs in manufacturing. The assumption among employees is that AMHS will replace them rather than enhance their productivity and the profitability of the business.
Also read: Pallet Truck: A Must for Safe and Easy Material Handling Business Operation