Pressure gauges are divided into two categories. We’ll discuss why you should get a liquid-filled gauge rather than a dry one. In the realm of industrial and commercial components, dry pressure gauges are the backbone. Take a look at the majority of air compressors. A dry gauge may be found on many industrial devices and some of the more expensive bicycle pumps. However, there are several disadvantages to using dry gauges.
Moisture in the gauge might cause the dial to get obstructed. The moisture in the gadget can turn to ice if the temperature goes lower enough, enabling the device to malfunction completely. When it comes to selecting a liquid filled pressure gauge, the option may appear straightforward. Whether it’s liquid-filled or not, the choice is yours. However, before selecting, consider the following variables to choose which gauge is best for you and your purpose.
High-stress pressure sites, such as quick and repeated loads, pressure peaks, and physical vibrations, are measured using liquid-filled gauges. Glycerin, or a mixture of glycerin and water, is frequently used to fill liquid-filled gauges. Depending on the circumstances you need the gauge for, you can choose from the various liquid-filled gauges.
Uses and Benefits of liquid gauges
Typical liquid-filled gauge is filled with 100% (99.7% min.) glycerin, which begins to get sticky at +17 degrees C and becomes slimmer as the temperature drops, causing the pointer to travel gradually to the right place. The gauge would cease working fully around -5 degrees Celsius. The ideal location for a standard gauge would be somewhere with a stable temperature that doesn’t change much.
Temperatures as low as -46 degrees C can be reached using liquid-filled gauges containing 2 parts glycerin and 1-part water. These gauges are appropriate for places when the temperature is shallow. This form of gauge, for example, may be considered in areas with severe winter temperatures. The majority of liquid-filled gauges are airtight, allowing them to function in caustic situations and withstand moisture ingress and ice.
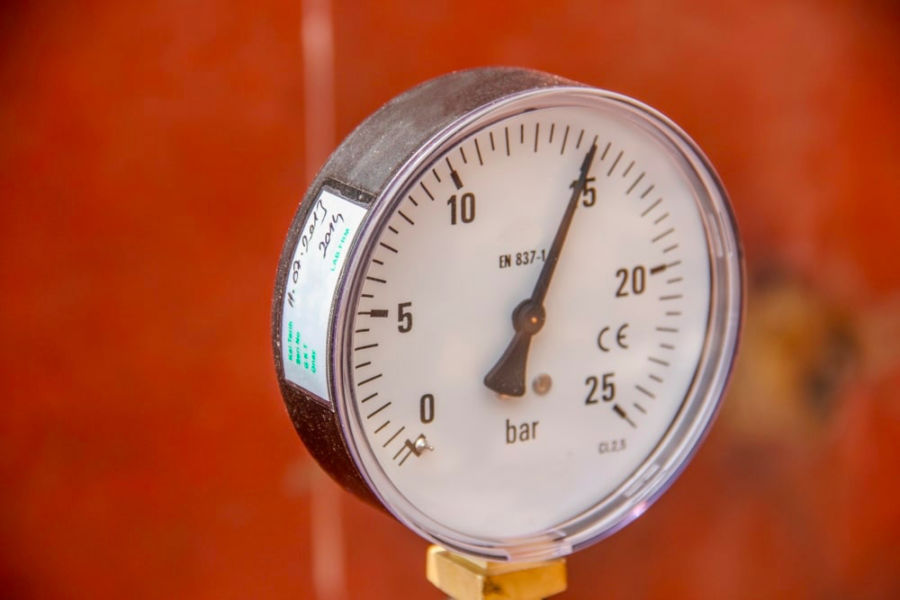
Glycerin-filled gauges are ecologically beneficial since they are non-toxic, non-harmful to water, and fully disposable.
Vibration is the most common cause of gauge failure. Vibration damages fragile links, pivots, and pinions in classic dry gauges, resulting in variable performance. The fluid fill efficiently dampens system pulsation in a liquid-filled gauge, making the gauge pointer clearer to see. Humidity and moisture, on the other hand, cause complications for dry gauges.
Condensation can make it harder to read a gauge and, in rare situations, create ice, which can fail. On the other hand, liquid-filled gauges are sealed to avoid internal condensation, and gauge movement is protected under icing conditions by holding moisture out of the system.
- Glycerin is generally used for room-temperature applications, while silicone oil is used for severe temperature applications, mainly when icing is an issue. If the system has uncovered electrical connections, an oil with insulating properties is suitable. Due to the in compressible viscous filling, liquid-filled gauges last longer than regular (non-hermetically sealed) gauges. This design benefit leads to increased efficiency over time owing to lower instrumentation costs and fewer unexpected outages.
- Internal liquids protect against extreme temperature variations and vibrations, which are essential causes of gauge failure. Temperature surges and vibrations are reduced as a result of their utilization.
- Condensation build-up causes sight concerns in classic gauges. This may be a critical (and expensive) flaw in high-humidity situations—an illegible gauge is a useless gauge. Our liquid-filled gauges aim to prevent moisture from penetrating not just the body covering but also the interior of the case lens, reducing the impact of high humidity settings.
- Liquid-filled gauges are often used in highly acidic chemical methods, production, or processing operations, and when items must be transported, stored, or handled under harsh temperature conditions since they are enclosed and built to fulfill rigorous criteria.
How to refill liquid in liquid-filled pressure gauges?
We recommend emptying, rinsing, drying, and then refilling to avoid having various layers of liquids.
Fill your gauge with glycerin, silicone, or mineral oil once it has been adequately drained, cleaned, and dried.
- Empty the gauge by removing the black rubber fill cap.
- Drain and dry the gauge after rinsing it with water. Continue till all the silicone has been extracted from the gauge.
- Glycerin, silicone, or mineral oil can be used to refill the bottle. Provide space for the liquid to spread as the gauge warms up by leaving an air bubble.
- Replace the rubber fill plug with care.
Although some clients are concerned about the cost of fluid filling a pressure gauge, the lengthy benefits are evident: greater safety from vibrations, pulsing, erosion, and humidity results in a more durable and dependable instrument.
Our liquid-filled gauges are highly robust, resulting in lower costs and improved precision over time. We also provide a variety of customizable process gauges, including gauges explicitly designed for the oil and gas sector.
Also read: Know What Trees Do For Humankind and Why Its Value is Beyond Calculation