This is a variation on traditional pressure die casting that uses a standard hydraulic press instead of heated metal, while still being able to use metal with relatively low melting points. The technique involves sealing the mold and placing it in a closed hydraulic press where molten metal is introduced under pressure. At this higher pressure, the boiling point of the liquid inside the mold is raised, leading to a more complete and even casting.
In cold chamber pressure die casting, molten metal is poured into a single-piece mold called a shot sleeve. As the liquid metal is poured into the shot sleeve, it is compressed and pushed forward by a piston which plows against the material just outside of the tip of the shot sleeve.
The cold chamber pressure die casting process is often used to produce small or delicate parts. The high pressure that is used in this process helps to ensure a high degree of accuracy and consistency in the part’s dimensions. Additionally, the use of a mold cavity allows for complex shapes to be created with ease.
One downside of the cold chamber pressure die casting process is that it can be expensive to set up and operate. Additionally, the process can be slow, and it is often limited to smaller parts. However, the quality and accuracy of parts that can be produced with this process is unmatched by most other manufacturing methods.
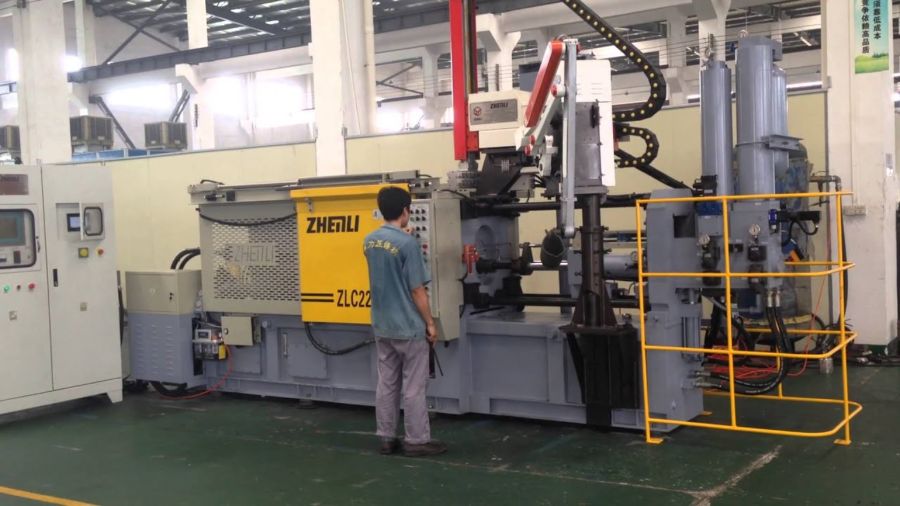
If you are looking for a manufacturing process that can produce high-quality, precision metal parts, then it may be the right choice for your business. This manufacturing process is best used to create small- and medium-sized metal parts, and it can ensure a high level of accuracy with complex designs. However, this process can be expensive and time consuming to set up and run, so it may not be a good choice if you are in need of larger quantities of parts.
If you are considering using the cold chamber pressure die casting process for your next manufacturing project, be sure to consult with an experienced and knowledgeable manufacturer to learn more about this process and how it can benefit your business.
It is one of the most common metal forming processes used in industry. This process involves forcing molten metal into die cast mold with both high-pressure and low-temperature.
The outcome of this process occurs when under certain conditions, the alloy (a mixture of different metals) undergoes solidification shrinkage during cooling, and then causes the mold to contract, which pushes the molten metal into the die under pressure.
The cooling phase that occurs in this process is because of a high-pressure gas, such as nitrogen or argon , which prevents the solidification shrinkage from occurring while also forming a protective atmosphere around the casting during its solidification phase.
Also, the gas pressure decreases as the metal fills the die to lessen the force of pressure against it so that it does not break from being under too much pressure.
The piston freezes any leftover liquid metal in place as it moves forward. This creates a slug of metal that is forced into the die cavity. The die cavity is then cooled to form the desired shape.
Compared to other types of die casting, this die casting has a higher forming pressure and can produce parts with more complex shapes. However, it also has a lower production rate and is more expensive to operate.
Also read: The Six Secrets to Making Lucrative Business Decisions You Should know