Globally, about 100 million tonnes of galvanized steel are manufactured each year, and consumption for high goods remains robust. Profitable items are those that are uniformly coated and manufactured economically. To do this, manufacturers of hot-dip galvanized strip work to optimize their production processes in terms of both quality and cost. Galvanized strip’s ultimate rate is determined by various factors, including the material’s surface, zinc adherence, and homogeneous coating weight thickness.
The first two stated parameters are controlled by appropriate substrate preparation and strip temperature management, but the third component, coating weight, is frequently determined too later in the procedure to be corrected. Coating weight thickness, paint depth dimensions and thickness values, or the dry film thickness abbreviated as DFT is a critical variable that affects the quality of the finished product, the control of the manufacturing process, and the cost of the product.
The thickness of any particular film can indeed be determined by selecting the appropriate mil gauge for the purpose. GGC, which stands for Global Gauge Corporation, was created in 1999 and purchased Measuray’s resources, launching the inaugural PLC-based instrument called X-Ray thickness gauge shortly after that. The global gauge has acquired established industry competitors throughout the years, most recently PDM Technologies and ESC Opportunities.
The global gauge has expanded its equipment portfolio and has supplied hundreds of thousands of new and upgraded gauges. Global gauge equipment collection is now widely acknowledged as the professional benchmark for non-contact width, depth, and thickness assessment technologies in rolling plants and processing units.
At Global Gauges, the thickness gauges for different types of steels and metals as well as other materials are well manufactured in order to provide the best measurement values along with accuracy and credibility. Here, customers find a reliable and efficient coating weight measurement gear with many diverse applications.
Automatic coating weight management is critical for consistent productivity with minimal zinc use on hot-dip galvanizing plants. Because performance differs from one coil to another coil, it is possible to regulate the transformation and improve yield by adjusting the air knife as well as procedure conditions.
This article outlines the optimum design for such a coating weight measuring and control system that continuously enhances its internal optimization techniques through a comparison of expected and measured coating weights.
This design assesses long-term changes in operation and automatically optimizes the controller’s behavior to changing production conditions by including coating thickness information from hot and cold sensing devices. Changes to the product are managed using a presetting system that automatically integrates data sets under “normal” production configurations. The “best” collection of information for that commodity is recommended for prospective production cycles.
Installations of such a coating weight regulator have demonstrated that production tolerances may be tightened while expenses are decreased. Assessments of primary coating material are included, as well as approaches for optimizing mill utilization by automatically adjusting production tolerances in response to changes in the target coating weight. Throughout product changes, these tweaks nearly eliminate scrap.
Repeated hot galvanizing is a cost-effective way to coat vast quantities of steel sheets using a zinc (alloy) coating. The procedure commences by central heating the steel and then immersing it in a pool of melted zinc and zinc amalgam, as illustrated in the following diagram.
The highest-quality items have a consistent coating weight and do not contain any uncoated strip segments. Because coated coils are acquired depending on a predetermined coating weight, loops with almost any undercoated sections, even a few grams per square meter, are classified as faulty goods, unable to be sold as stipulated, resulting in economic losses.
The simplest way to minimize material costs connected with the covering is to use the least amount of zinc necessary to achieve the product standard. Regarding development and capacity building downgrading costs, as noted previously, the goal is to tighten operational tolerances as near to the lower standard as possible to decrease zinc utilization.
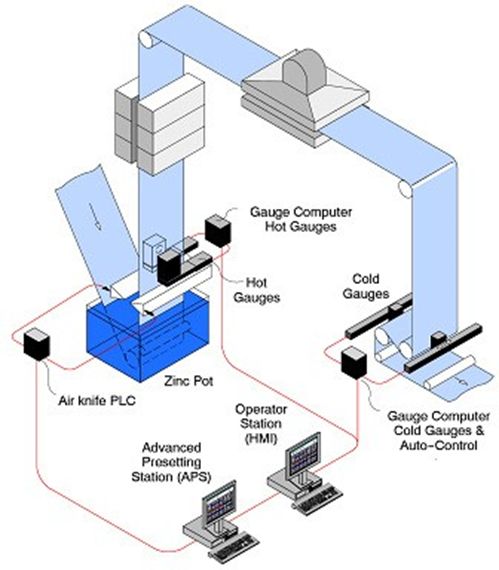
Figure 1: A Hot Dipped Galvanizing abbreviated as HDG process shows measurements taken using a cold gauge and then a hot gauge
Most still rely upon Weigh-Strip-Weigh (W-S-W) guidelines recommended in ASTM A90 and ISO 1460 to validate the weight of hot-dip zinc coatings. Whereas this technology provides direct accuracy and consistency to accredited international laboratories, it is only possible once the coil departs the machine. If the findings are unsatisfactory at this phase, the whole coil must permanently be degraded or trashed.
When testing is conducted on the very first loop of the latest campaign, operational modifications are frequently established well just after the second coil has already begun, significantly increasing discarded product. Galvanized items with asymmetrical coverings necessitate more attention and time during the W-S-W process, extending the time required to apply any rectification.
The thickness dimensions of the dry film (DFT) or covering is undoubtedly the most critical measurement done during the preparation and examination of protective coatings. When sprayed only within the DFT range indicated by the manufacturing company, layers are intended to accomplish their intended function. Proper paint thickness guarantees that the product performs optimally.
Even the most precise elementary specification will involve the measurement of DFT. The term “coating weight” pertains to the percentage of zinc coating tailored to the specific surface region of a product. There are two distinct ways of determining the covering weight of the particular hot-dip galvanized steel.
The first approach for determining the coating weight has been the weigh-galvanize-weigh procedure, which is only suited for single specimens. This procedure weighs a steel component once it has been cleansed and again when it has been galvanized. The Weigh-galvanize-weigh measures only the increased zinc weight throughout the coating.
However, because the layer is composed of combined iron and zinc, this approach underestimates the overall sealant weight by 10 percent. Additionally, measuring and calculating the contact area of complicated steel construction can be challenging, making coating weight calculations even less precise.
Weigh-strip-weigh has been the second technique for determining coating weight, yet it is also destructive, making it suitable only for sole specimens. This procedure weighs a galvanized object immediately after chilling, removes all or most of the zinc protective coating, and weighs it once more. The part’s contact area then splits the weight variation to determine the proportion of zinc coating applied during hot-dip galvanizing.
This procedure deems a part useless due to the fact that it completely destroys the covering even during the assessment. Weigh-strip-weight is typically employed on small items, including nails, and is inexact though once the zinc coating has been stripped, a part of base metal is also stripped. Due to the additional iron that may have been included in the calculation, the accurate zinc coating weight would be underestimated.
The Performance Indicator
Regular layer thickness measurements aid in controlling costs, operation efficiency management, finish quality maintenance, and contract specification adherence. Manufacturers specify target parameters for achieving the best performance qualities, and customers expect these criteria to be reached.
Handheld Gauges for coatings thickness
Many users are unaware of the tremendous relevance of coatings in an enterprise. Frequently, certain goods attain operation solely through the treatment of a particular layer. These coatings provide a variety of activities: they provide an aesthetic finish, provide corrosion protection, and perform mechanical functions. As a result, the coating is subjected to rigorous requirements.
Just as critical as the covering itself is testing the thickness immediately during the product’s manufacturing. This is achieved with the use of a compact coating thickness gauge. The above ensures cost-effectiveness and efficient functioning. If the coating is too thinner, the product is doomed to fail. If, for example, an excessive amount of gold is added to printed circuit platforms, material costs skyrocket.
Nevertheless, not only during manufacture but also throughout the duration of ships, aircraft, as well as other safety-critical equipment, other safety-critical elements of the system must be continuously tested using just a particular coating thickness analyzer. This provides assurance that the finish and components continue to meet the standards.
Several well-reputed companies have been manufacturing diversified accurate and precise Width gauges. Some of them, along with their key features, are listed below:
Applications for Metals thickness as well as Coating Weight Assessment
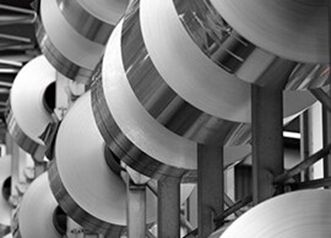
Applications for Aluminum Thickness as well as Coating Weight Estimation
The non-contact measurement equipment for hot or even cold Aluminum rolling mills ensures accurate, repeatable readings throughout the high production of the Aluminum plate and sheet, including foil, irrespective of alloy and clad stack concentration.
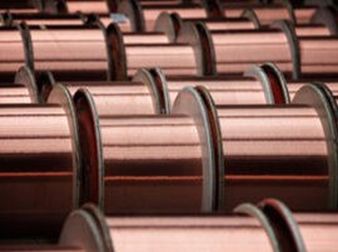
Applications for Non-Ferrous Metals dimensions such as Thickness and Coating Weight Estimation
Non-contact gauging equipment from Global Gauge is designed for specialty metals rolling machines to deliver consistent and accurate thickness observations, enabling you to create high-quality solutions while minimizing raw material utilization.
Also read: 4 Easy Steps to How You Select A Mattress for Your Electric Adjustable Bed