According to different application environments, optical modules can be divided into data center and carrier levels. The telecom market has harsh and harsh use environments. It requires high reliability. Data center-level optical modules have lower performance requirements than carrier-class modules, such as temperature requirements, but also have the characteristics of high speed requirements, rapid iteration, and large demand. Thus, telecom operators require a packaging process that is more suitable for the needs of the data center market.
Common Optical Module Packaging Types
The basic structure of the optical module package is the optical transmitting side module (TOSA) and the driving circuit, the optical receiving side module (ROSA), and the receiving circuit. The process of packaging the laser and detector into TOSA and ROSA is the core and main part of the optical module packaging. technical barriers. The packaging process types of TOSA/ROSA mainly include: TO-CAN coaxial packaging, butterfly packaging, COB packaging, BOX packaging, FlipClip, etc.
The TO-CAN package is an airtight package. The laser die and the backlight detection tube are bonded to the heat sink, and are interconnected with the outside by bonding. They are mainly deployed in 10G optical modules.
Butterfly package integrates semiconductor laser, refrigerator, thermistor and other components in a metal package. Couple the optical signal emitted by the laser to the fiber through a certain optical system for various speeds and distance transmission.
The BOX package is a butterfly package used for multi-channel parallel packaging. It can be made into airtight and non-airtight packages. It is applied for medium and long-distance high-speed optical equipment transmission, which is relatively expensive.
COB package is a chip-on-board package. The laser chip is directly attached to the PCB, which saves the PCB area. Due to the construction of a shorter interconnection path, the performance is also improved. The COB package is more suitable for 100G QSFP28 optical modules, such as 100G QSFP28 SR4, LR4, ER4, etc.
Chip-on-Board (COB) Packaging Process
Next, the article will introduce how to realize the COB package. The technological process of parallel optical modules COB packaging is shown in the figure below.
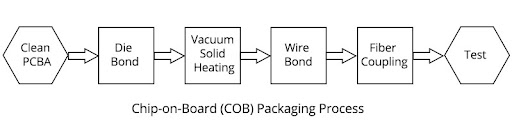
Before packaging, it is necessary to clean the PCBA pasted with electronic components (PCBA is the PCB pasted with electronic components such as resistance and capacitance), so as to avoid the influence of oil, dust, and other attachments on the PCB on the bonding, and then affect the qualification rate and product performance. To avoid damage to the PCBA, it is best to use a plasma cleaning machine for cleaning.
After cleaning the PCBA, the bonding operation will be carried out next. With the help of bonding equipment, the optoelectronic chip will be connected with the pad on the PCB to form a system with complete electrical performance. The main process operations of bonding are positioning patches and wiring. The first patch operation that needs to be positioned is die bond. First, apply silver paste on the position where the PCB needs to be pasted, and then position the chip at the position where the patch is needed. The positioning of the optical chip will directly affect the optical coupling effect. According to the experiment and analysis, the general accuracy requirement is 3 ~ 5 μ m.
Heat curing treatment is required to fix the chip after pasting it. In order to prevent the oxidation reaction at high temperatures from affecting the chip function, the method of vacuum nitrogen thermal curing is generally adopted. The baking time is determined according to the time requirements of silver paste thermal curing.
After baking, take out the PCBA for wire bond operation and connect the photoelectric chip pad with the PCB pad with gold wire. The quality of the wiring will affect the high-speed signal transmission performance of the product, which will lead to the improvement in the bit error rate of the product or the quality of the transmitted signal.
Next, the PCBA with gold wire will be fiber-coupled. As mentioned earlier, at the transmitting end, the light emitted by the VCSEL laser is coupled to the optical fiber. At the receiving end, the light transmitted through the optical fiber is coupled to the photosensitive surface of the PD device.
Finally, the performance index of the packaged optical module is tested to judge whether it meets the requirements.
Why Is the COB Packaging Process More Suitable for Data Center 100G Optical Module?
1. Save volume and meet high density requirements. The traditional single-channel 10Gb/s or 25Gb/s rate optical module adopts SFP package to weld the electrical chip and TO-packaged optical transceiver components to the PCB board to form an optical module. For a 100Gb/s optical module, when using a 25Gb/s chip, four sets of components are required. If an SFP package is used, it will require four times the space. COB packaging can integrate TIA/LA chip, laser array and receiver array in a small space for miniaturization.
2. The process itself is suitable for mass production and meets the requirements of large demand and low cost. COB packaging directly adheres the laser chip to the PCB, eliminating the need for complex packaging steps, reducing production costs. Mass production becomes simpler with the maturity of related technologies and equipment operations. In contrast, TO- CAN packaging and BOX packaging rely more on manual power.
3. Compared with other packages, it has outstanding advantages. TO-CAN packaging is more suitable for low-speed optical modules, with mature technology and high yield, but it is not suitable for mass production. Butterfly packaging has high cost and is more suitable for fields with high requirements for lasers and reliability, such as carrier-grade optical modules.
It should be noted that there are still technical difficulties in the precise positioning and bonding of chips by COB packaging. Besides, the yield rate of optical modules is not optimal, so QSFPTEK paid special attention to the performance testing of optical modules.
Conclusion
On the whole, COB packaging meets the requirements of high reliability and low cost, and is the mainstream packaging type of 100G QSFP28 optical modules. Facing the problem of product yield, QSFPTEK has strictly controlled the product quality of 100G QSFP28 optical modules. Control, through multiple optical and compatibility testing procedures to ensure the pass rate of the optical module.
Also read: 40G QSFP+ DAC Cable vs Transceiver: QSFP 40G DAC Twinax Copper Cable vs QSFP SR4 Transceiver